Alkali recovery system
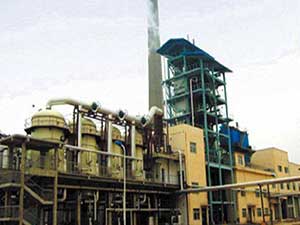
Alkali recovery system is the most efficient way to solve the black liquid problem currently.
After black liquid extraction, evaporation, combustion and causticization, the SS, COD, BOD in the black liquid can be wiped put completely. And the akali can be recycled in the same time. The steam can be reproduced though this process. However, alkali recovery has a high technical requirement so the equipment need a high investment. Thus, the alkali recovery system is mainly for large pulp and paper industry at present. In addition, the grass paper pulp can create high silicon content white mud, it can cause secondary pollution.
After black liquid extraction, evaporation, combustion and causticization, the SS, COD, BOD in the black liquid can be wiped put completely. And the akali can be recycled in the same time. The steam can be reproduced though this process. However, alkali recovery has a high technical requirement so the equipment need a high investment. Thus, the alkali recovery system is mainly for large pulp and paper industry at present. In addition, the grass paper pulp can create high silicon content white mud, it can cause secondary pollution.
Bleaching tower
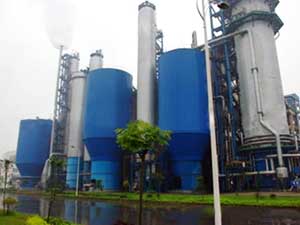
The bleaching tower can be divided to up-flow bleaching tower and the downward flow bleaching tower.
It is a common equipment in the paper making industry. The tower adopts a cylindrical structure, the pyramid of the tower is a pyramid in certain angle. At the bottom of the pyramid, there is a screw conveying device. In general, the pulp has a tendency to fall down under the action of gravity, so even the screw conveyer is short, the efficiency of discharging pulp can keep high. This is energy saving and the pulp in the bleaching tower falls in an equal speed, which can ensure the bleaching performance.
It is a common equipment in the paper making industry. The tower adopts a cylindrical structure, the pyramid of the tower is a pyramid in certain angle. At the bottom of the pyramid, there is a screw conveying device. In general, the pulp has a tendency to fall down under the action of gravity, so even the screw conveyer is short, the efficiency of discharging pulp can keep high. This is energy saving and the pulp in the bleaching tower falls in an equal speed, which can ensure the bleaching performance.
Desander
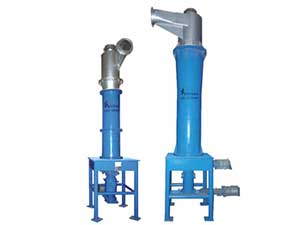
Desander is used for separate the metal, sand and other impurities in the paper pulp.
It is an ideal equipment for getting high quality pulp and the essential machine to process waste paper. Desander is composed of feed tee piece, outlet pipe, big cone, shell, and sediment tank. Desander separates the fiber and impurities according to their weight. The equilibrium water pressure in the bottom is slightly higher than the pulp pressure, so that the fiber can't go into the sediment tank. Only sand, prill, gommures, plastics and other impurities can go into the sediment tank. In this way, the fiber loss is reduced.
The desander can be used single or multi series if the production capacity is relatively great.
Before you open the desander, please turn on the high pressure valve in the bottom, fill the sediment tank and the scummer with water, then turn on the pulp pump.
Observe the pressure gauge on the pulp pipe, adjust the flow control valve, and make the inlet and outlet pressure difference meet the process requirements.
It is an ideal equipment for getting high quality pulp and the essential machine to process waste paper. Desander is composed of feed tee piece, outlet pipe, big cone, shell, and sediment tank. Desander separates the fiber and impurities according to their weight. The equilibrium water pressure in the bottom is slightly higher than the pulp pressure, so that the fiber can't go into the sediment tank. Only sand, prill, gommures, plastics and other impurities can go into the sediment tank. In this way, the fiber loss is reduced.
The desander can be used single or multi series if the production capacity is relatively great.
Before you open the desander, please turn on the high pressure valve in the bottom, fill the sediment tank and the scummer with water, then turn on the pulp pump.
Observe the pressure gauge on the pulp pipe, adjust the flow control valve, and make the inlet and outlet pressure difference meet the process requirements.
Johnson screen
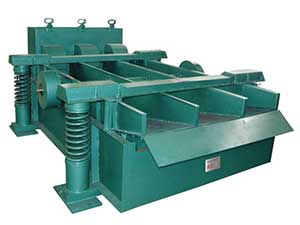
Johnson screen is a kind of screening device with a vibrating sieve plate.
The vibration can break the fibrous layer on the sieve plate, then the broken fibers go through the sieve pore. Pulp screen is a process of the fiber layer forming and breaking.
Johnson screen is used for removing the impurities such as the knot, the raw stock, the batten in the pulp and the sand, stone chips came with raw materials. After the pulp cooking process, the pulp goes into the Johnson screen, the screen can protect the equipment in the following process.
Johnson screen has the advantages of high knot removing capability, energy saving and small footprint. It is an ideal equipment for paper pulp sieving.
The vibration can break the fibrous layer on the sieve plate, then the broken fibers go through the sieve pore. Pulp screen is a process of the fiber layer forming and breaking.
Johnson screen is used for removing the impurities such as the knot, the raw stock, the batten in the pulp and the sand, stone chips came with raw materials. After the pulp cooking process, the pulp goes into the Johnson screen, the screen can protect the equipment in the following process.
Johnson screen has the advantages of high knot removing capability, energy saving and small footprint. It is an ideal equipment for paper pulp sieving.
Pressure knotter
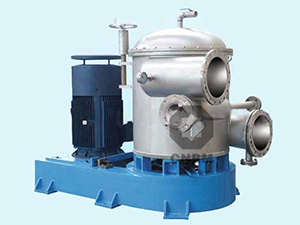
Pressure knotter is used for removing the larger materials which are not digested, and it can remove the heavy impurities such as the metal block and dinas.
The pressure knotter has the advantage of wide range of application, it can be used in all kinds of knot removing in chemical pulping process. Pressure knotter adopts the spinning small-bore screen cylinder, it can save energy and improve the capacity at the same time. The surface of the screen cylinder is covered by a high abrasion resistant coating which adopted the latest technology and can prolong the service life of the screen cylinder. Pressure knotter adopts the internal flow pulping structure, has the dual functions of knot remving and impurity removing. The impurities won't hurt the blade, and the operation is safe and reliable. The sieve drum adopts an unique sealing structure which has good sealing effect and can prolong the pressure knotter's service life.
The pressure knotter has the advantage of wide range of application, it can be used in all kinds of knot removing in chemical pulping process. Pressure knotter adopts the spinning small-bore screen cylinder, it can save energy and improve the capacity at the same time. The surface of the screen cylinder is covered by a high abrasion resistant coating which adopted the latest technology and can prolong the service life of the screen cylinder. Pressure knotter adopts the internal flow pulping structure, has the dual functions of knot remving and impurity removing. The impurities won't hurt the blade, and the operation is safe and reliable. The sieve drum adopts an unique sealing structure which has good sealing effect and can prolong the pressure knotter's service life.
Pressure screen
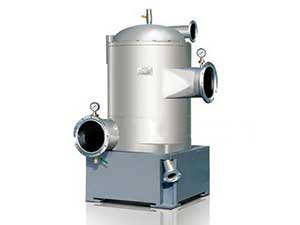
Pressure screen is used for closed thermal screening process of chemical wood pulp, straw pulp, reed pulp,and the riddling and fine screening process of waste paper pulp and mechanical pulp.
Pressure screen has the advantages of energy saving, water saving, simple processes, high yield and high screening efficiency. The precision welding process improved the resistance of the screen cylinder. And the latest plating technology improved the dimensional accuracy of the screen cut and the abrasion resistance of the screen cylinder.
Pressure screen has the advantages of energy saving, water saving, simple processes, high yield and high screening efficiency. The precision welding process improved the resistance of the screen cylinder. And the latest plating technology improved the dimensional accuracy of the screen cut and the abrasion resistance of the screen cylinder.
Pulp board machine
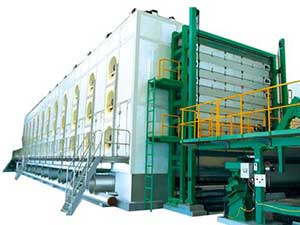
Pulp board machine is used for making market pulp board.
This kind of pulp board machine use wood pulp, cotton pulp and bamboo pulp as raw materials, produce goods pulp board in different specifications. After the pulp board machine, there is a pulp board cutting machine. Pulp cutting machine cut the pulp board into blocks for packing and transporting.
The basic parts of the pulp board machine are forming, pressing, drying and flow delivery system.There is no essential difference between pulp board machine and paper making machine on the shape, structure or other aspects.The forming machine use back net, also can use long net. Usually, the drying part is dryer. The difference between the paper machine and the paper board machine is the forming wire. The forming wire of pulp board machine has larger neteye. And for the pulp board machine, the dry temperature can't be too high, so the quality of the pulp board won't be affect.
The pulp flow into the machine from the forming part, then on a special blanket, the pulp will be pressed by the roller press. After that, the squeezed pulp goes into the rotary dryer to evaporate the water. The blower will take the moisture out and there you get the dried pulp board.
This kind of pulp board machine use wood pulp, cotton pulp and bamboo pulp as raw materials, produce goods pulp board in different specifications. After the pulp board machine, there is a pulp board cutting machine. Pulp cutting machine cut the pulp board into blocks for packing and transporting.
The basic parts of the pulp board machine are forming, pressing, drying and flow delivery system.There is no essential difference between pulp board machine and paper making machine on the shape, structure or other aspects.The forming machine use back net, also can use long net. Usually, the drying part is dryer. The difference between the paper machine and the paper board machine is the forming wire. The forming wire of pulp board machine has larger neteye. And for the pulp board machine, the dry temperature can't be too high, so the quality of the pulp board won't be affect.
The pulp flow into the machine from the forming part, then on a special blanket, the pulp will be pressed by the roller press. After that, the squeezed pulp goes into the rotary dryer to evaporate the water. The blower will take the moisture out and there you get the dried pulp board.
Pulp diffusion tube
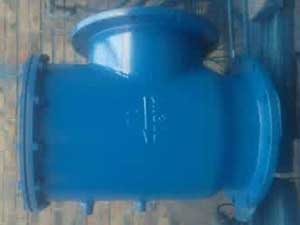
Pulp diffusion tube is a cylindrical vertical container.
The container has a nozzle and a nozzle arm. Fluid such as cleaning fluid flow into the pulp through the nozzle. At the same time, the container has a coaxial filter and mesh arm to discharge the filtrate. At the outer end of the strainer, the discharge tube is arranged in a vertical alignment. The discharge pipe can slip through control and is sealed with the outlet of the filtrate.
The container has a nozzle and a nozzle arm. Fluid such as cleaning fluid flow into the pulp through the nozzle. At the same time, the container has a coaxial filter and mesh arm to discharge the filtrate. At the outer end of the strainer, the discharge tube is arranged in a vertical alignment. The discharge pipe can slip through control and is sealed with the outlet of the filtrate.
Regulating device
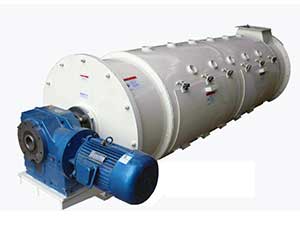
The regulating device is equipped with a double-axle differential speed tuner.
It adopts multi-point admission, features long time, good quality, and high degree of maturation. The two shafts of the regulating device are different in diameter and rotate speed. This allows the material, the steam and the liquid to be whisking under two axles, fully shearing and mixing. The adjustment time of the regulating device can be up to 180 seconds, which can ensure the full aging of the material. It is also stable in the water. All material contact parts in the regulating device are made of stainless steel. The regulating device adopts the large opening structure to facilitate the operation and maintenance. The angle of the blade can be adjusted. The regulating device has the correct pelletizing parameters and the special cutter structure, which is more suitable for making small pellets. The regulating device is mainly composed of blade and nozzle. Steam, molasses or water is usually sprayed into the regulating device, and the longer it adjust, the better product you'll get.
It adopts multi-point admission, features long time, good quality, and high degree of maturation. The two shafts of the regulating device are different in diameter and rotate speed. This allows the material, the steam and the liquid to be whisking under two axles, fully shearing and mixing. The adjustment time of the regulating device can be up to 180 seconds, which can ensure the full aging of the material. It is also stable in the water. All material contact parts in the regulating device are made of stainless steel. The regulating device adopts the large opening structure to facilitate the operation and maintenance. The angle of the blade can be adjusted. The regulating device has the correct pelletizing parameters and the special cutter structure, which is more suitable for making small pellets. The regulating device is mainly composed of blade and nozzle. Steam, molasses or water is usually sprayed into the regulating device, and the longer it adjust, the better product you'll get.
Get In touch Now!
Leave messages for quotations and solutions. The average response time is up to 24 hours. Your privacy is protected. Check privacy policy here.