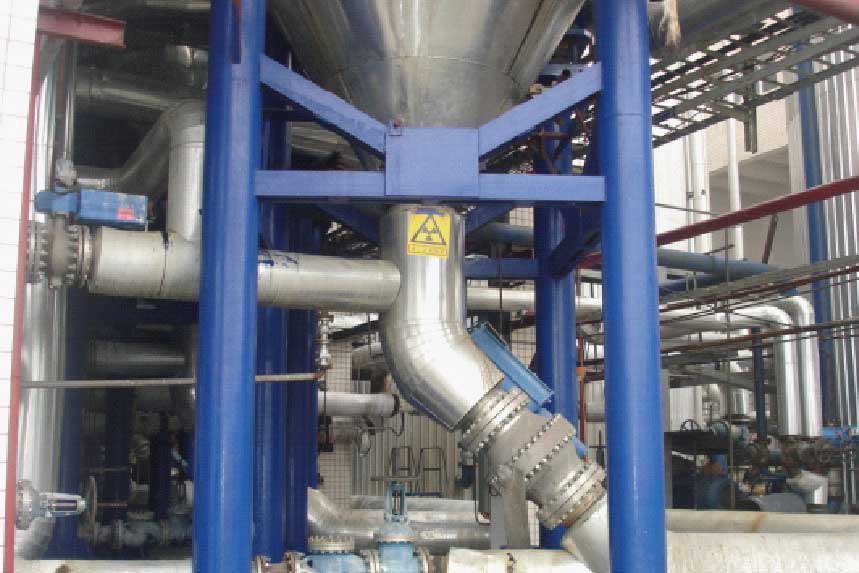
displacement digesting system
- The high degree of energy saving, environmental protection and automation is the main advantage of DDS cooking.
- Per-ton pulp of steam consumption is reduced greatly to 0.6-0.8t (Conventional consumption is 2.0-2.5t).
- Pulp has gotten better bleaching. Its low Kappa number and high strength are conducive to oxygen delignification, reduction of consumption of chemicals for bleaching and reduction of pollution.
DDS cooking evolved from the RDH cooking (Rapid Displacement Heating). It adds the tank system and divides the cooking process into several steps. The cooking liquid replaced by each step is classified and stored in the tank area for subsequent cooking. The high degree of energy saving, environmental protection and automation is the main advantage of DDS cooking.
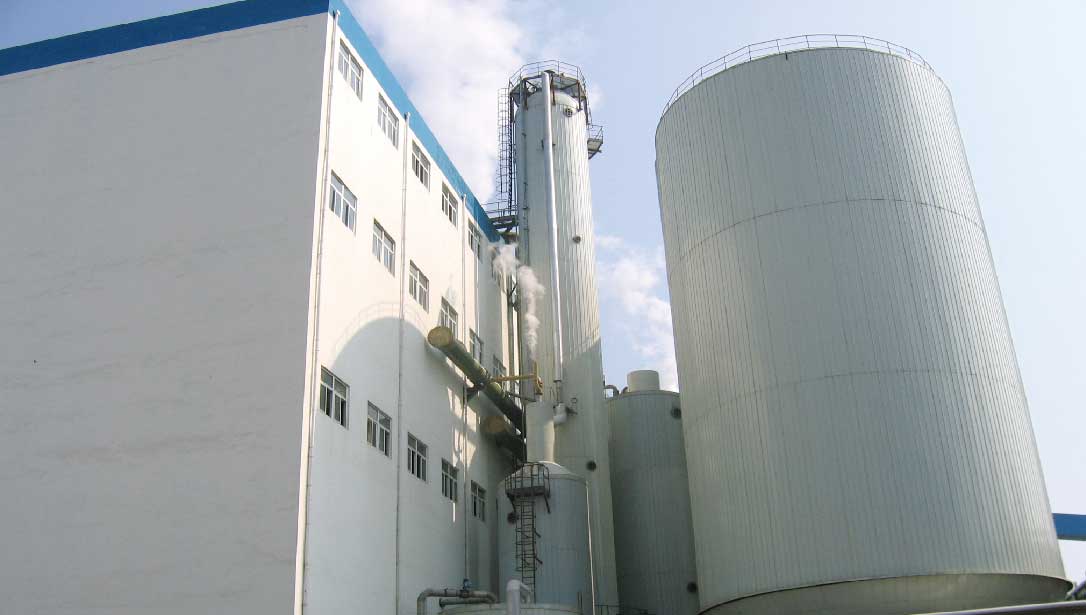
Displacement digesting system we offer
Displacement cooking is that used cooking liquor is displaced by cooking liquor or washing water using the principles of displacement cycle and diffusion washing of black liquor in the batch digester. Both used cooking liquor and heat are displaced, and then cold spraying is fulfilled.
Displacement cooking can make full use of the black liquor repeatedly, extract lignin from the cooking system in delignification phase and dissolve hemi-cellulose. During the supplementary delignification phase, cooking liquor can be refilled. By the principles, initial heat and chemicals can be recycled. The cooking can keep continuous balance during the whole cooking process, which can help to improve pulp quality and production efficiency.
-
Digester
At present, the world's traditional cooking system is cooking digester centered. DDS cooking digester are optimized and formed on the basis of traditional cooking digester. CNBM is very mature in manufacturing cooking digester.
Due to the different process, on the basis of the traditional cooking system, DDS digester increased automatic valve, convulsions system, vacuum system, gamma rays, blow tank dilution mouth, cone tripod, filling nozzle, and the steam distributor etc.
Model ZJG3 ZJG4 ZJG5 ZJG6 ZJG7 ZJG8 ZJG9 Effective volume (M3) 110 135 175 225 250 330 400 Diameter (internal) (mm) 3600 4000 4500 4500 4500 5600 5800 Design pressure (Mpa) 0.9/1.2 Design temperature (℃) 180/240 -
Heat exchanger
-
Black/white liquor heat exchanger , white liquor heater
Black/white liquor heat exchanger and white liquor heater adopts horizontal tube type heat exchanger. Black/white liquor heat exchanger is single heat transfer, white liquor goes through the shell side while the black liquor goes through the tube pass. White liquor heater adopts the dual process heat exchange, white liquid goes through the tube pass, steam goes through the shell side. -
Spiral plate heat exchanger used in turpentine system
DDS cooking turpentine recovery system adopts spiral plate heat exchanger for cooling and recovery of gasification turpentine, and four spiral plate heat exchangers are used for recycling twice.
-
Black/white liquor heat exchanger , white liquor heater
Displacement digesting system working principle
DDS cooking is divided into six steps: pot (LC), primary cooking (IC), intermediate cooking (MC) heating and heat preservation (FC), replacement and recovery (RC), blow (DC).
DDS cooking process principle is using different temperature fluid for replacement, finally finished cooking in the form of cold discharge cycle, so that the heat and the residual chemicals can be fully used.
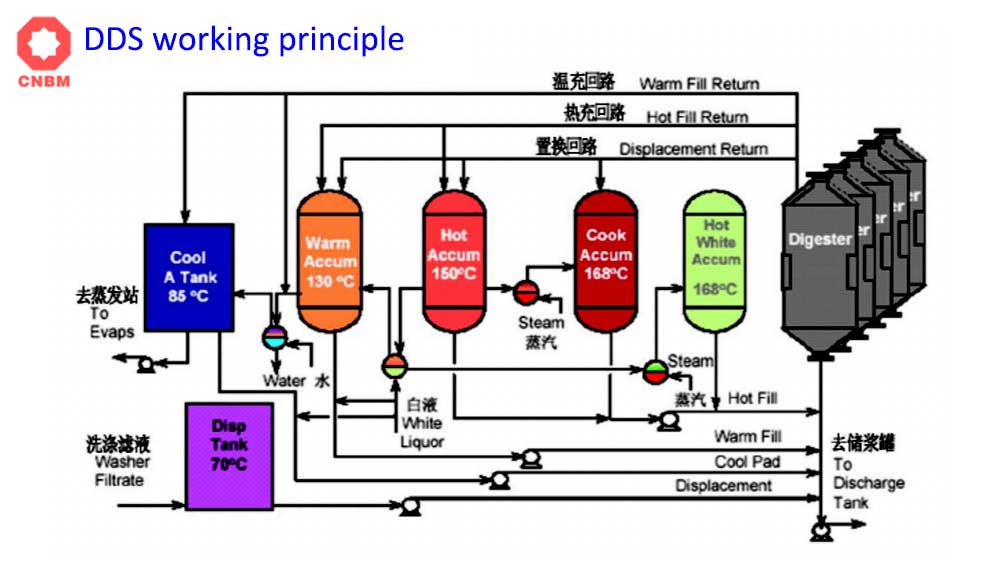
Displacement digesting system advantages
Displacement cooking technology is the most advanced batch cooking technology in the world nowadays. Compared with conventional cooking, it has the following advantages:
- Per-ton pulp of steam consumption is reduced greatly to 0.6-0.8t (Conventional consumption is 2.0-2.5t).
- It can achieve low Kappa number, high strength and high yield pulp through deep delignification.
- Pulp has gotten better bleaching. Its low Kappa number and high strength are conducive to oxygen delignification, reduction of consumption of chemicals for bleaching and reduction of pollution.
- Production process is controlled by microcomputer, which reduces manual operation as much as possible and keeps the system reliable and stable.
Leave messages for quotations and solutions. The average response time is up to 24 hours. Your privacy is protected. Check privacy policy here.