Overview of Paper Pulp Cooking Digester
The paper pulping digester is the main equipment for making chemical paper pulp. Digesters are mainly used to cook paper raw materials (such as wood, grass, rags, etc.). In the digester, paper pulp materials react with cook agent, and become paper pulp which is mainly cellulose.
Paper pulp digester category
Because of the differences of chemical pulping methods, fiber raw materials and paper industry production scales, the chemical paper pulping equipment is different. According to the operation process, chemical paper pulp cooking equipment can be divided into the batch cooking production line and the continuous digester. The digesters of batch cooking production line is globe digester or spherical digestger and cooking pot. The rotary globe digester is mainly used as the equipment for cooking the alkaline, sulfate or neutral salt paper pulp. Digester is a kind of vertical fixed equipment. Because of the differences of the corrosive action of cooking agent, process characteristics, structure, form and volume, the digesters are usually divided into sulfate cooking digester and sulfite cooking digester. Generally, the paper pulp cooking digester is large, it is usually used in large or medium scale paper making industry.
In addition to the main equipment, the batch chemical pulping equipment should be equipped with necessary auxiliary equipment, such as circulating pump, liquid medicine circulating heater, waste heat recovery equipment and blow tank.
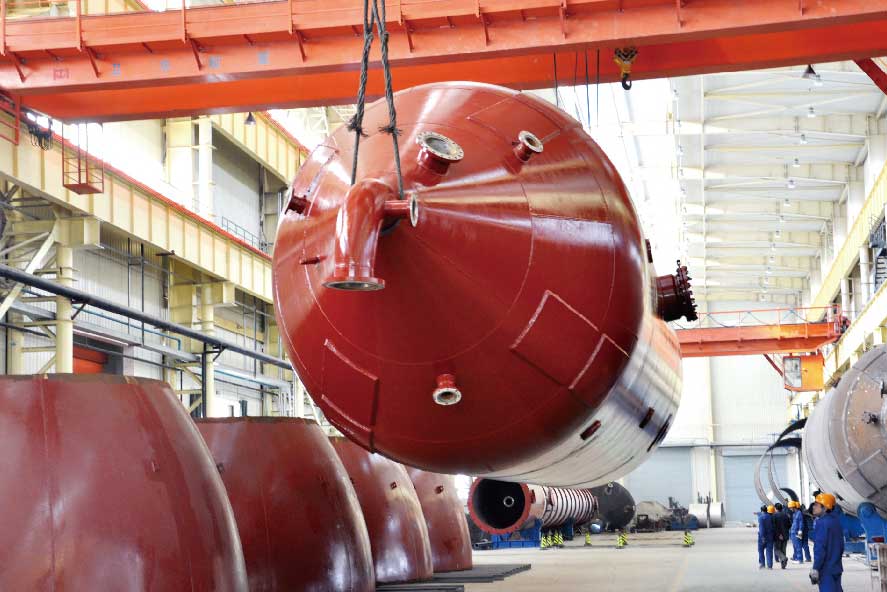
Continuous chemical pulping equipment can be divided into tower (or vertical) continuous cooking pot, also known as Camille continuous cooking pot and Pandiya horizontal tube and inclined tube continuous cooking pot according to main cooking equipment. The tower continuous cooking pot is suitable for large and medium-sized wood pulp paper making industry, and it is widely used in the world. The chemical pulping equipment used in pulping and papermaking industry in China is used in addition to large tower continuous cooking digesters.
The selection of chemical paper pulper machines is mainly based on investment, production scale, fiber material type, etc. The volume and number of paper pulping digesters are determined by the production scale, the type of cooking pot, the cost of equipment and the comprehensive balance of production. The size of wood pulp produced under 300t/d is best used in large and medium batch cooking digester, because the investment cost of batch cooking pot is 13% to 20% lower than that of continuous cooking digester under 300t/d. The wood pulp production is above 300t/d, and the continuous cooking digester should be selected. The production of non-wood fiber raw pulp is generally used in continuous cooking digester. This is mainly the stable quality of the pulp of continuous cooking, and the yield coefficient [t/(m3d)] is much larger than the batch cooking.
The working principle of various cooking digesters
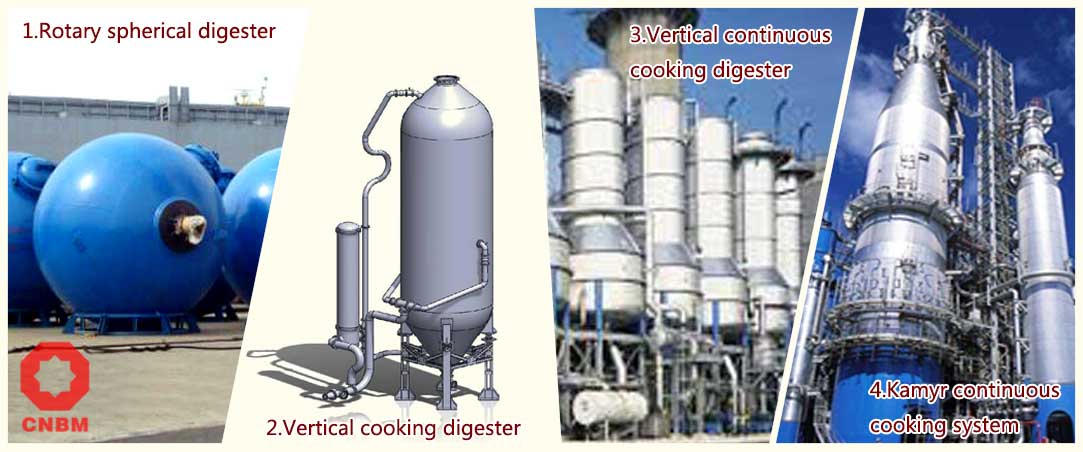
-
Rotary spherical digester
The steamed ball is a kind of rotary batch cooking equipment. It is spherical, mainly composed of sphere, machine seat, transmission device etc. The spheres are welded or riveted by steel plates. The position of the center line of the center of the ball is to open the filling hole for filling and feeding the cooking liquid. Steam and drain condensate from the hollow shaft through the steam heating. Steaming ball has the advantage of raw materials with liquid can be fully mixed, the quality of the pulp is evener, low liquid ratio, solution concentration is higher, can shorten the cooking time, simple equipment, less investment, easy to maintain and management. The disadvantage is that the area is large, direct steam, and the concentration of liquid medicine changes greatly. Steamed balls are less used in China. -
Vertical cooking digester
The steam of a certain pressure is used as the heat source (or electric heating can be used). The vertical paper pulping digester has the characteristics of large heating area, high thermal efficiency, uniform heating, short boiling time of night-material and easy to control heating temperature, etc. The inner layer of CNBM paper pulp cooking digester (inner pot) is made of acid-resistant and heat-resistant austenitic stainless steel. It is equipped with pressure gauge and safety valve. It features beautiful appearance, easy to install, easy to operate, safe and reliable. But with the development of science and technology, the equipment is updated. The current use has been phased out. -
Vertical continuous cooking digester
Vertical continuous cooking digester is the most widely used continuous cooking equipment in both domestic and abroad. By 1990, 350 sets of vertical continuous cooking digester had been in operation all over the world, and the total production and concatenation accounted for 45% of the alkaline pulping production in the world. Camille continuous cooking digester has undergone two major stages of technological development since it was put into the production. In 1958, the technology of cold spray was developed, that is, 70 to 80 degrees black liquor was injected into the bottom of the paper pulp cooking digester, which reduced the temperature of the pulp to about 85 degrees, thus improving the strength of the pulp. In 1962, the domestic high temperature counter current washing was successfully studied, which greatly improved the washing efficiency and simplified the washing equipment. -
Kamyr continuous cooking system
Kamyr or Camille continuous cooking digester has great adaptability to various cooking methods and raw materials. In addition to being mainly used in Kraft cooking, it can also be used in acid sulfite, acid sulfite and prehydrolytic Kraft processes to produce bleached pulp, dissolving pulp, primary color pulp and semi-chemical pulp. Raw materials are from coniferous to broadleaf wood, sawdust and grass fiber raw materials. At present, the types of Camille continuous steaming digester include liquid phase type, steam liquid phase type, high pressure prepreg and steaming point pot suitable for grass raw materials, etc.-
Camille liquid cooking digester
Camille liquid cooking digester is the earliest and most common form for industrial production. It is characterized by the fact that the cooking pot is filled with medicinal liquid, the liquid is relatively large, and the pressure in the pot is kept at 300 to 400 KPA higher than the saturated vapor pressure corresponding to the cooking temperature. This type is used for Kraft wood pulp cooking, its cooking process and co-heating are basically carried out intermittently. -
Camille steam-liquid cooking digester
The structure of the steam-liquid cooking digester is similar to that of the liquid digester, but the reverse top separator is used to replace the top separator of the liquid-phase paper pulp cooking pot. Chips from high-pressure feeders sent through the upper circulation tube are separated from the solution before entering the cooking digester. A vapor space is maintained at the top of the cooking digester so that the infiltrated wood chips can be heated quickly to the cooking temperature by direct steam, which means that there is no special soaking area in the cooking pot. This kind of cooking digester can be used in acid hydrogen sulfite method, hydrogen sulfite method, neutral sulfite semi-chemical method and pre-hydrolytic sulfate cooking method. -
Cooking digester with high pressure preimpregnation (double steam-liquid boiling pot )
The double-pot steam-liquid phase cooking digester is developed on the basis of a single steam-liquid phase cooking digester, and a vertical high-pressure preimpregnating digester is added between the high-pressure feeder and the cooking digester. -
Modified Camille continuous cooking digester (MCC)
MCC technology is dividing the cooking area into two parts: downstream and countercurrent cooking areas. In the downstream cooking area, the temperature is 169 ℃, and the countercurrent cooking area is 171℃, and then the countercurrent diffusion washing is carried out and the cold spray is carried out as usual. The temperature of countercurrent washing area is 140 ℃, and the kappa number of coniferous Kraft pulp is 25. EMCC technology extended the countercurrent cooking part to the countercurrent diffusion washing area, and the whole system was cooked at the same temperature at 160 ℃, and the kappa number of coniferous Kraft pulp was 17.
-
Camille liquid cooking digester
-
Horizontal tube continuous cooking digester
Foreign horizontal tube continuous cooking digester Pandia is the most commonly used paper pulp cooking equipment. Horizontal tube continuous cooking equipment can improve the quality of straw raw materials, dry and wet preparation process, as far as possible to ensure the quality of wheat straw pulping. The removal rate of conventional dry preparation pulping process is only 15%, which is more than twice as high as that of dry and wet preparation process. The improvement of dust removal rate can effectively protect the operation of cooking, washing and bleaching equipment, reducing the amount of chemicals, reducing the load of washing and bleaching process and the dust content of pulp, especially for wheat straw, the removal rate of silicon content can reach more than 15%. It can effectively reduce the interference of silicon to alkali recovery process and improve evaporation efficiency. Horizontal continuous cooking digester can also reduce the use of alkali pulp cooking, fast speed, low steam consumption.
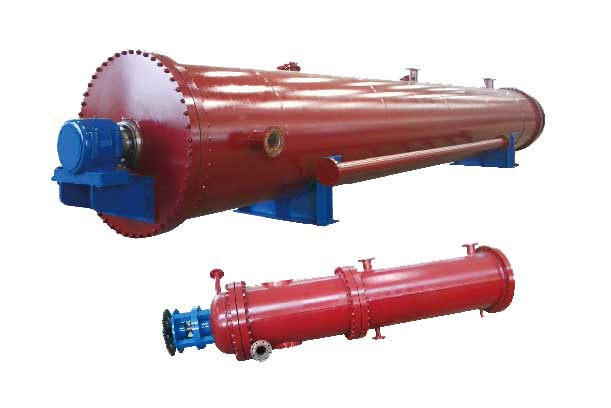
CNBM paper pulp digester advantages
Paper pulp cooking digester is the leading product of CNBM, we can produce all kinds of paper pulping digesters, including 50M3, 75M3, 110M3, 135M3, 175M3, 225M3, 250M3, 400M3, and series cooking digesters for paper pulping workshop and paper making industry. Maximum diameter 5, 8 meters, with a maximum capacity of 400 cubic meters. In view of the difference between alkaline pulp and acid sulfite pulp, the cooking pot is made of carbon steel structure, composite steel structure and duplex stainless steel.
CNBM provides paper pulper machines and turnkey project for paper making industry. CNBM is the leading manufacturer for paper pulping equipment in China. Our products are quality and reliable. Please leave messages for details and quotation.
Leave messages for quotations and solutions. The average response time is up to 24 hours. Your privacy is protected. Check privacy policy here.